News
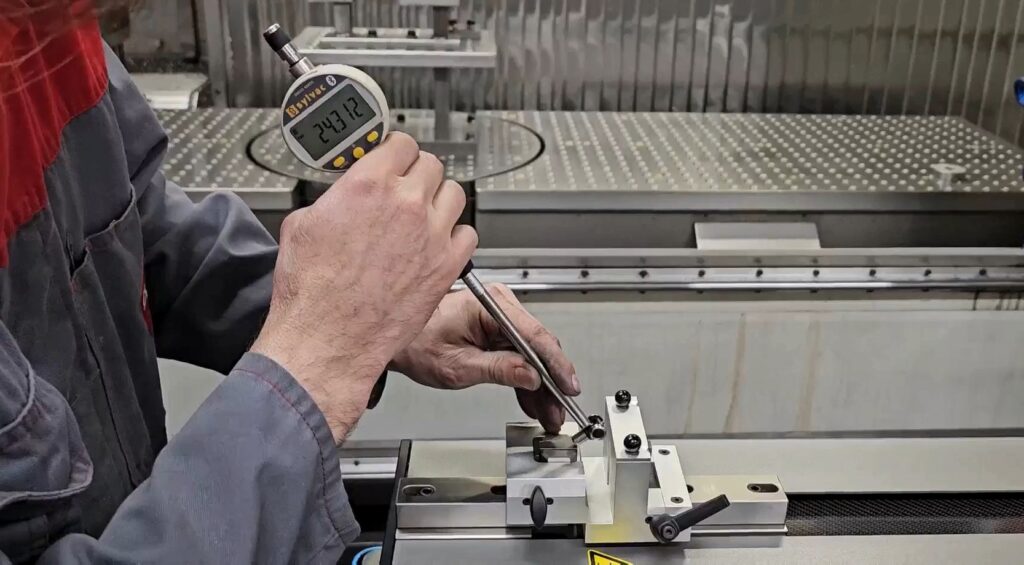
Introducing the HS3
26.05.25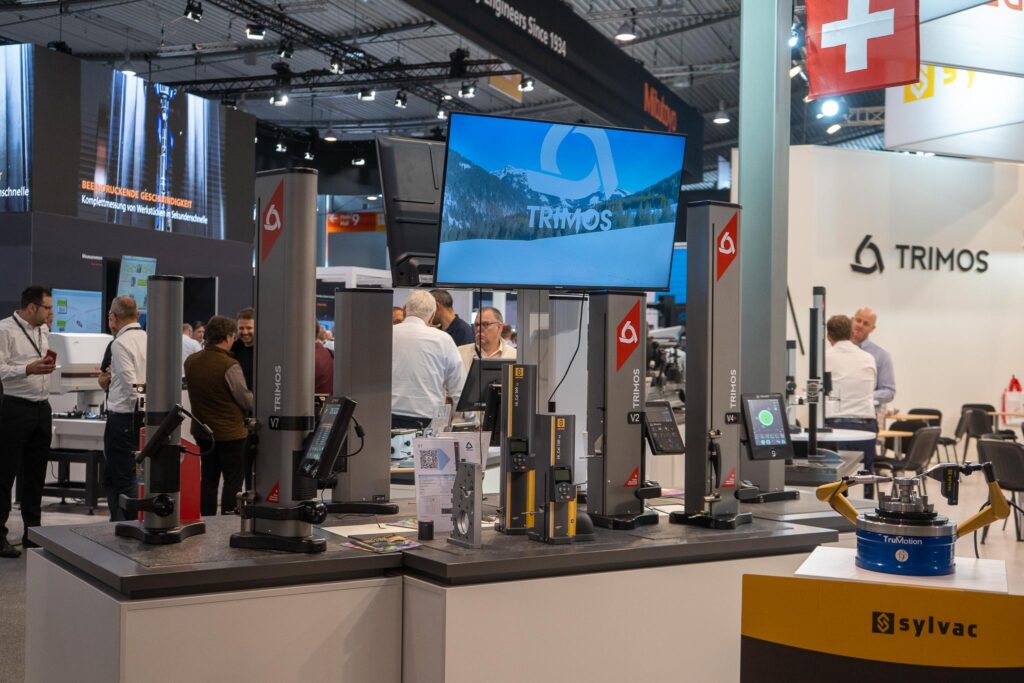
Control Show 2025
22.05.25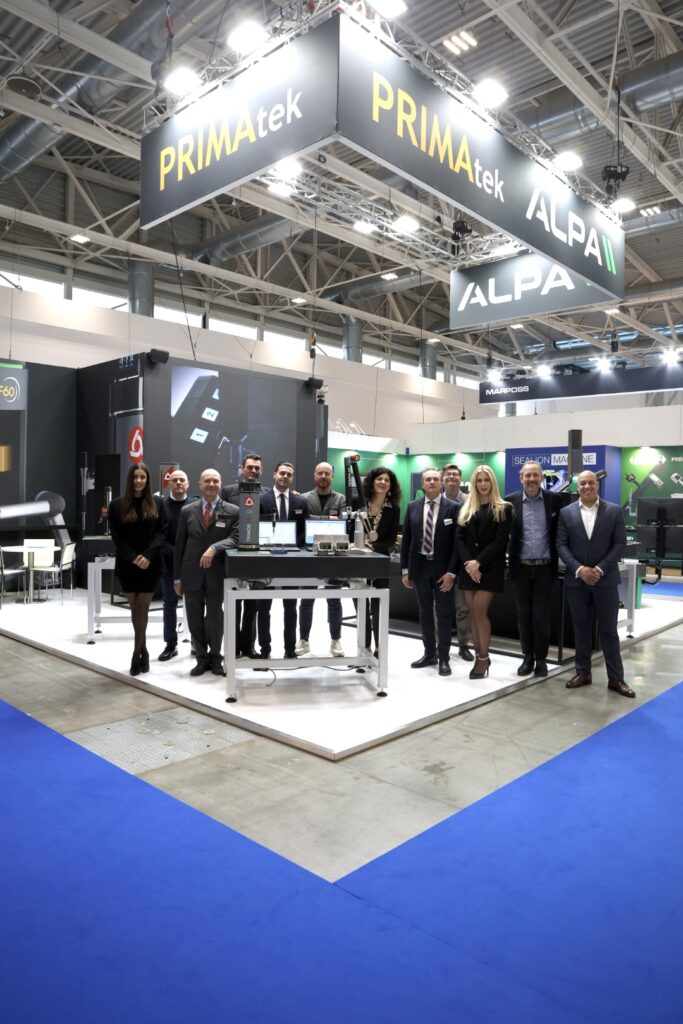
Exposition at MECSPE in Italy
10.03.25
F1 Car Manufacturing with Trimos precision
25.02.25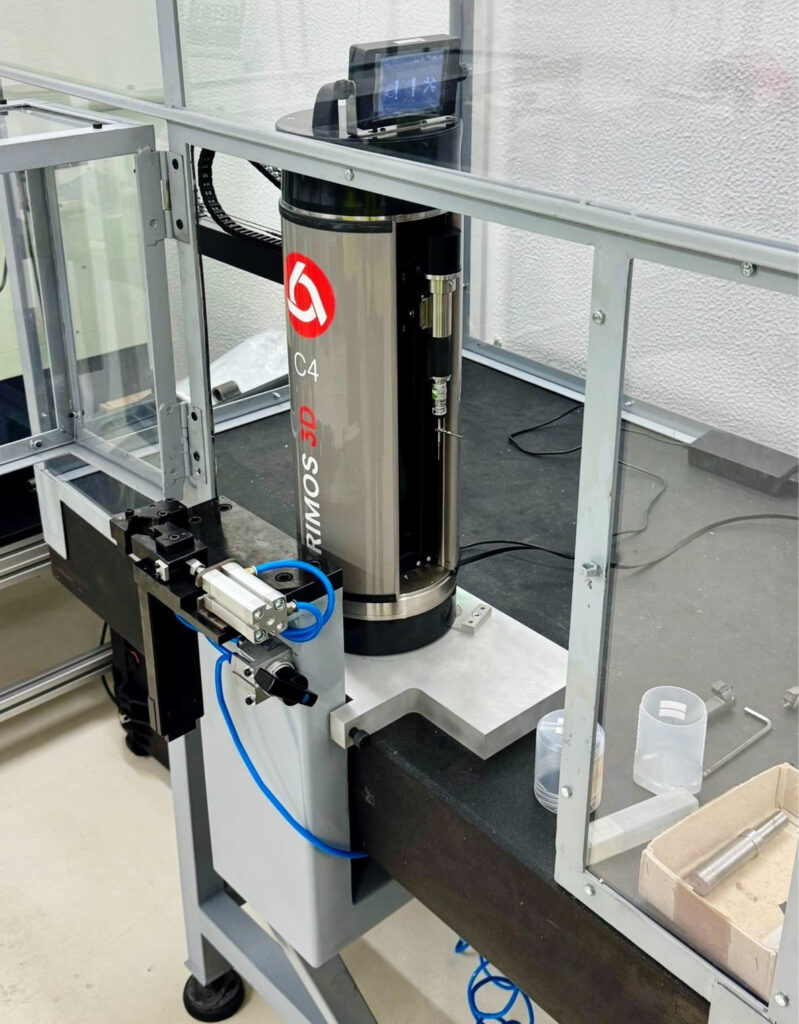
High-precision measurements in any workspace
17.02.25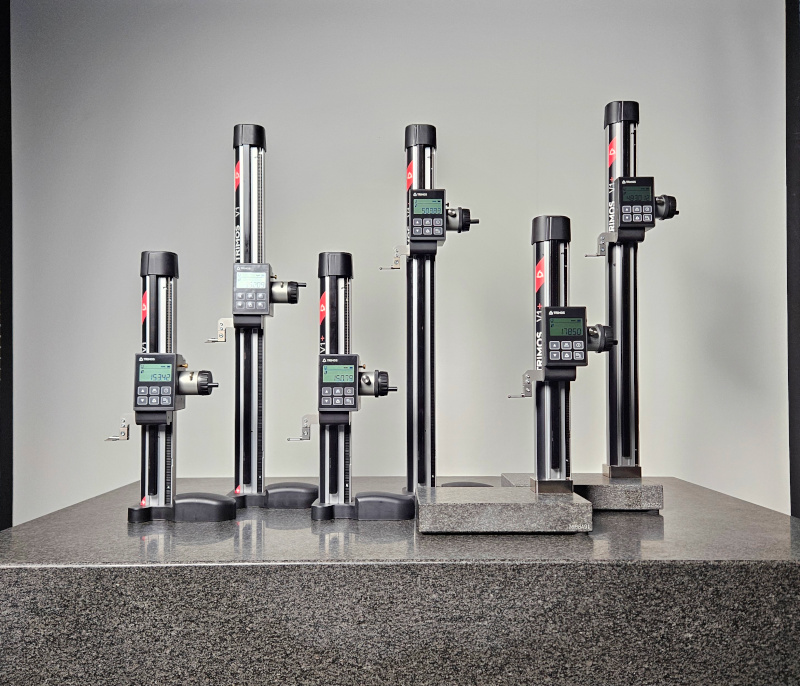
Tough gauges for the modern workshop
13.12.24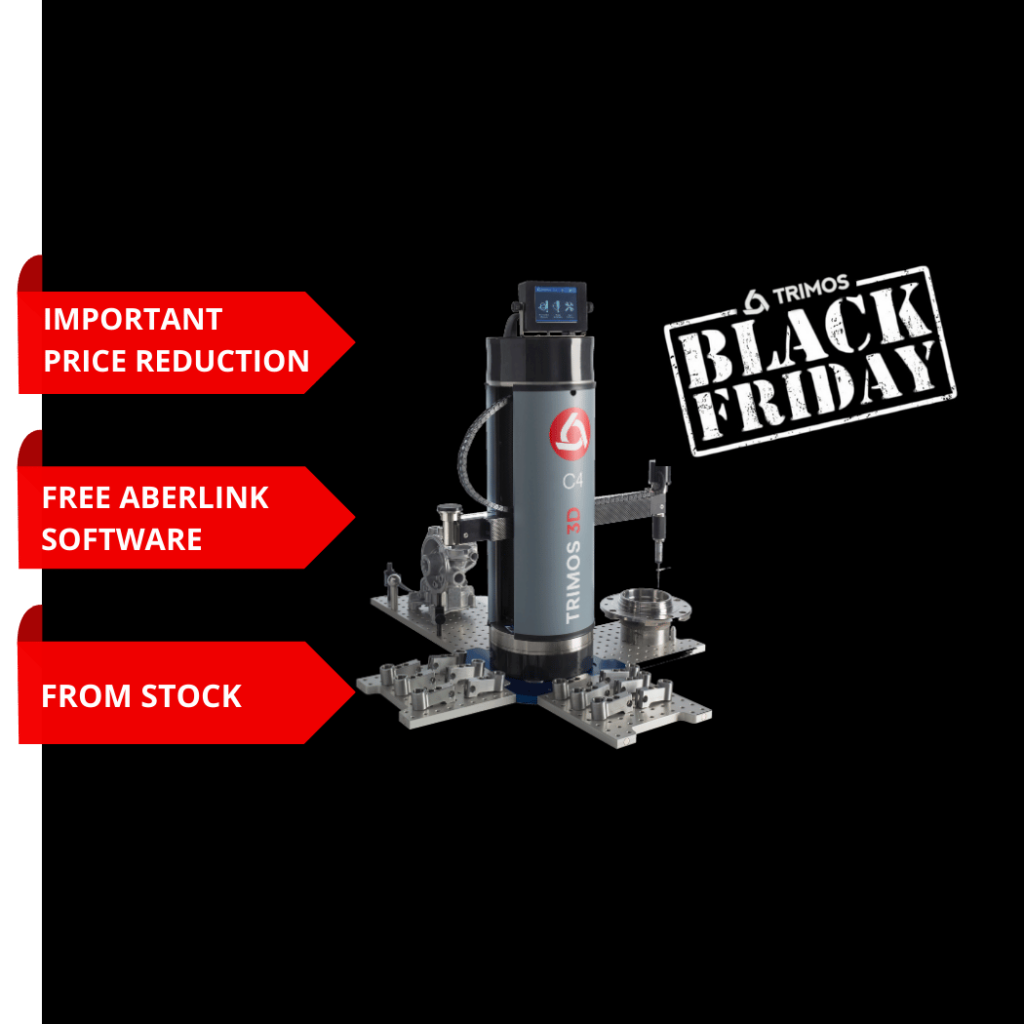
Black Friday 2024
27.11.24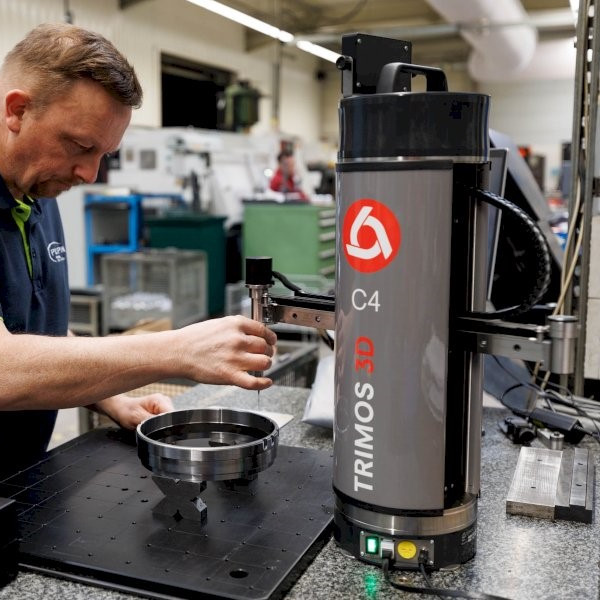
Easy 3D measurement in the Workshop
26.09.24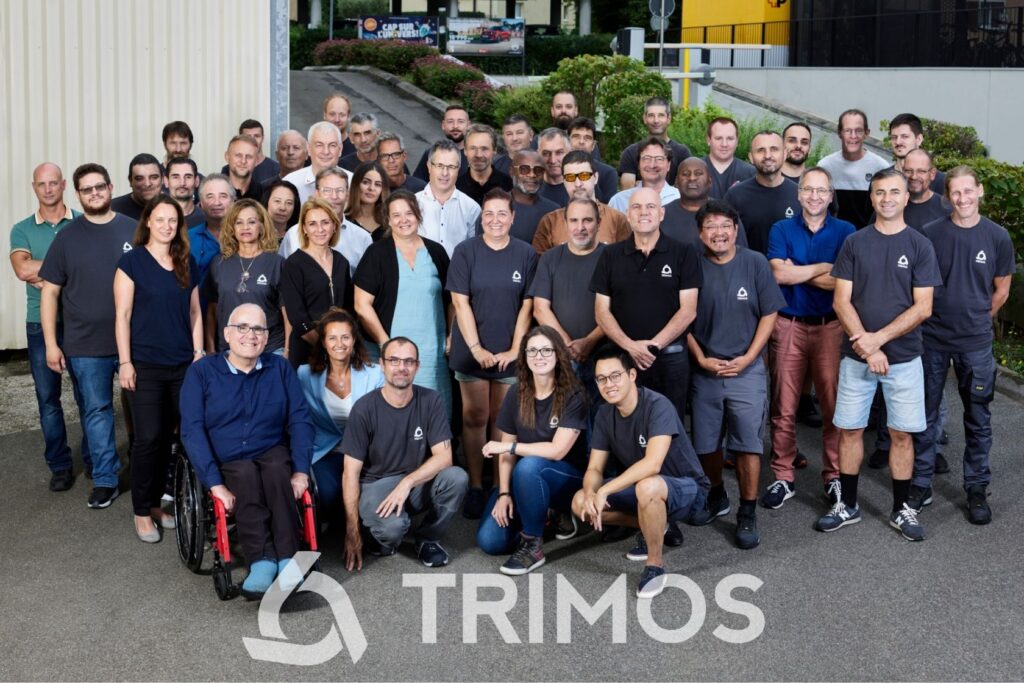
The Great Team behind our Precision
17.09.24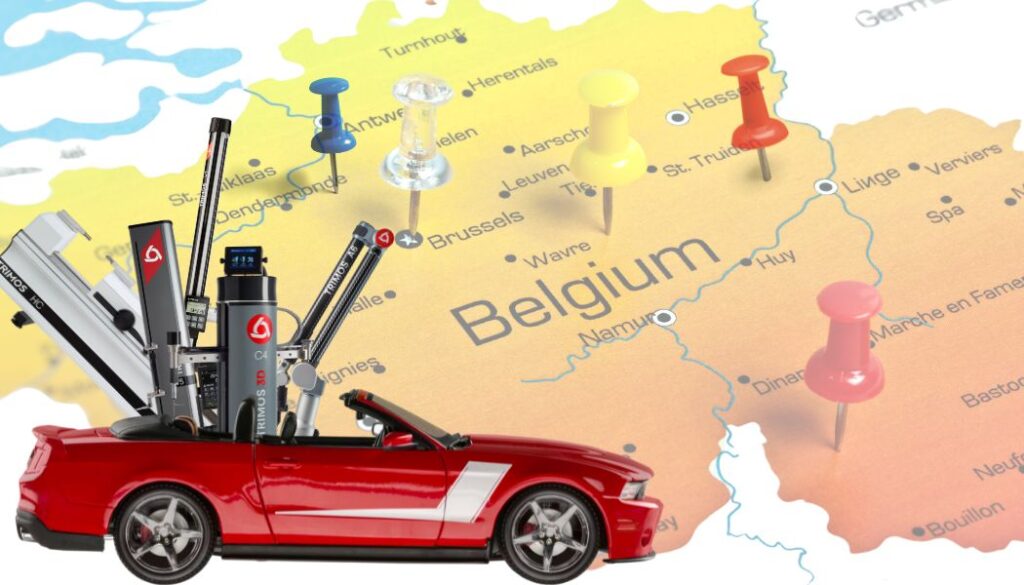
Dimensional metrology roadshow – Belgium
1.09.24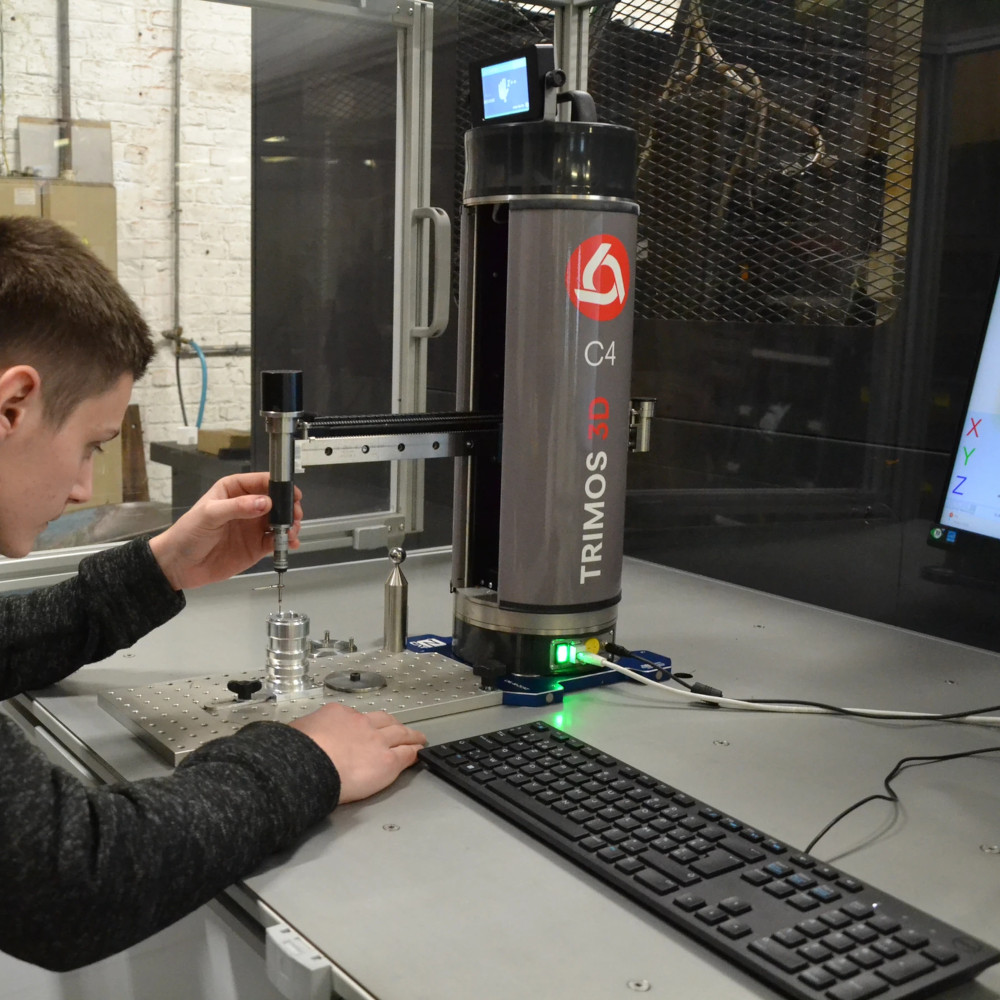
Dimensional control of machined parts
14.05.24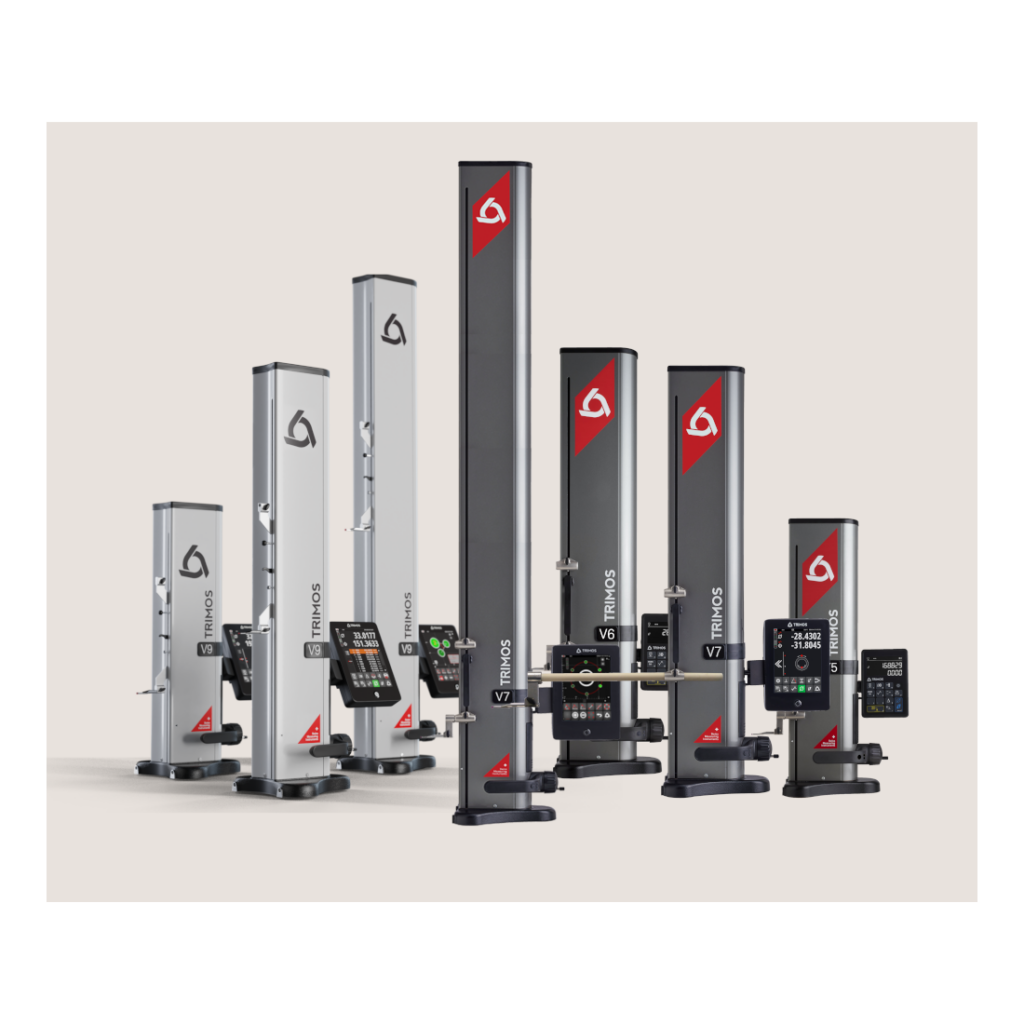
Height gauge selector
13.02.24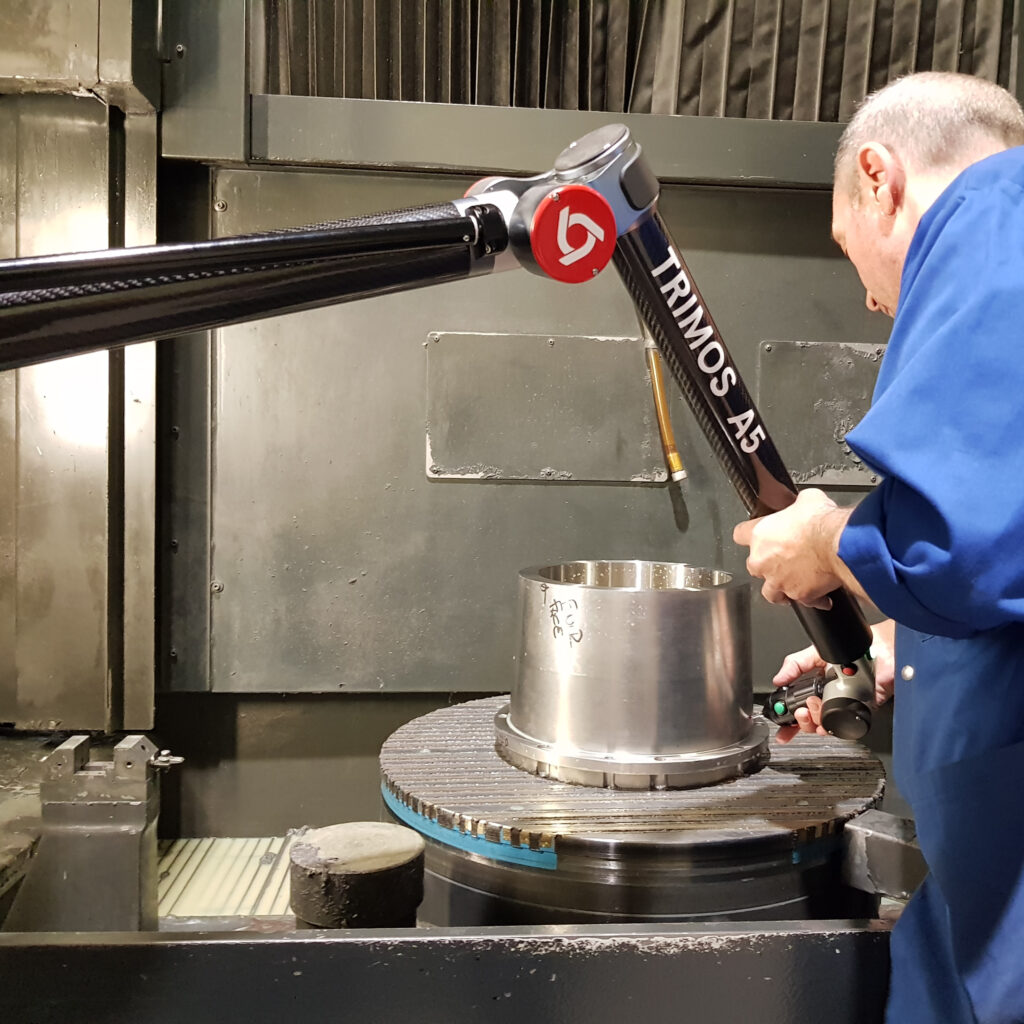
Precision and Efficiency in Metalworking
2.02.24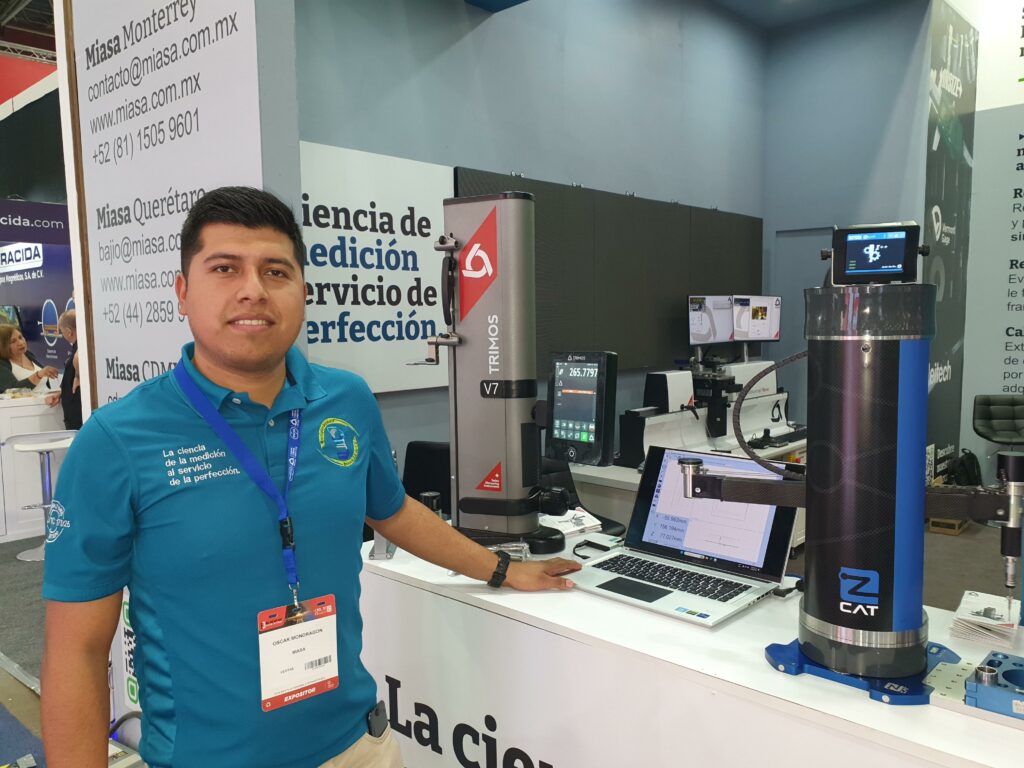
Expo Manufactura in Monterrey
30.01.24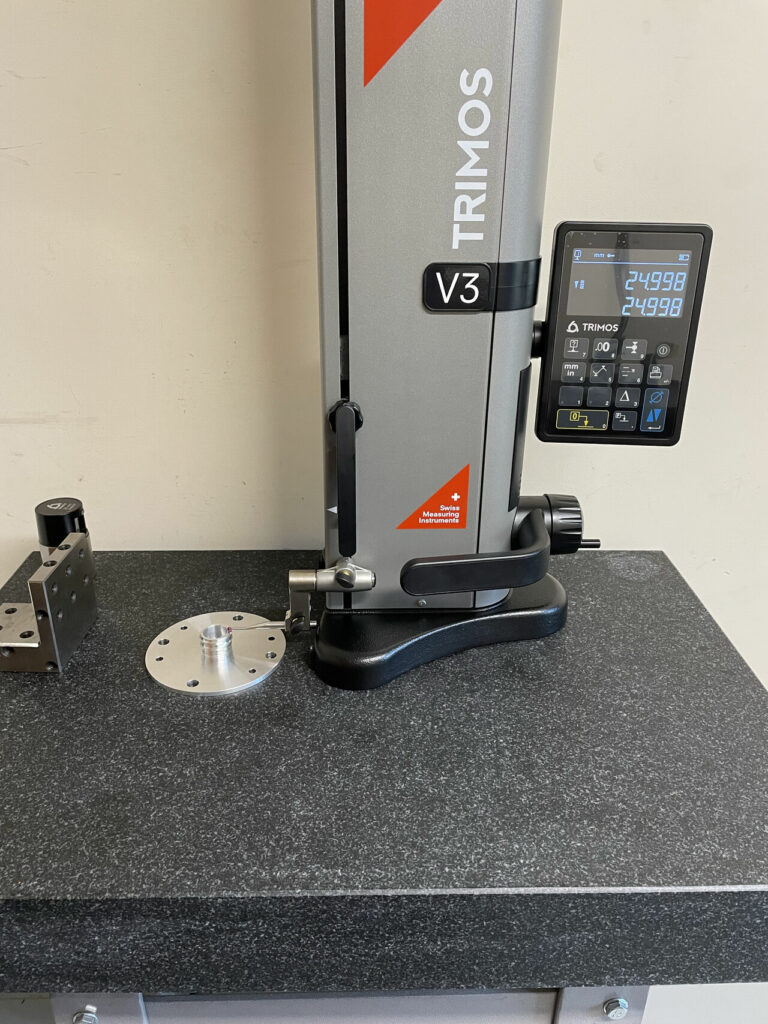
Increased Inspection Capability
15.12.23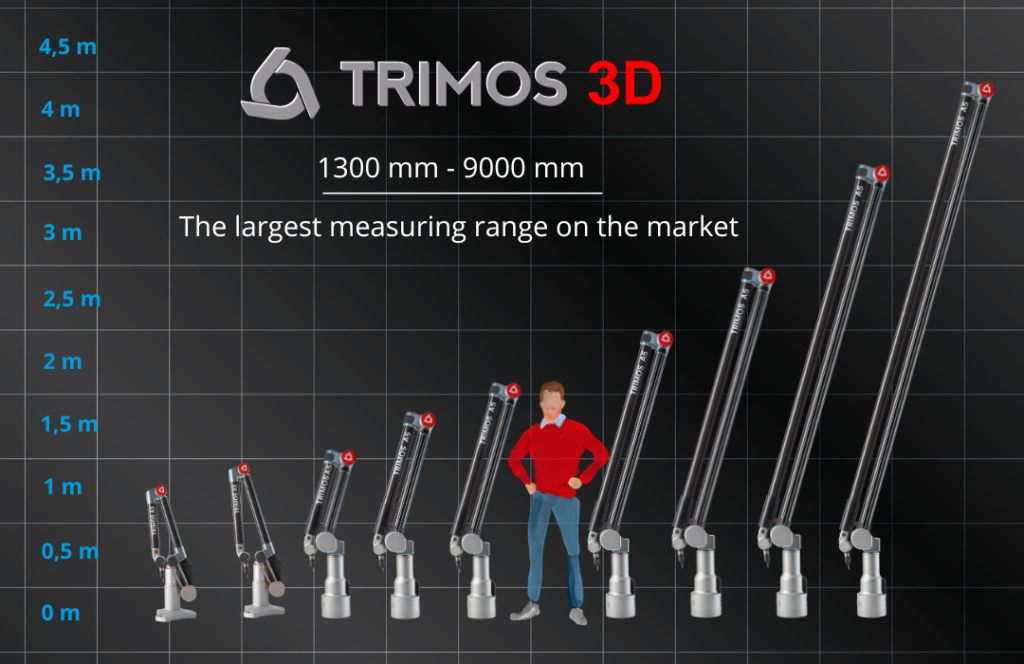
The largest measuring range on the market
14.11.23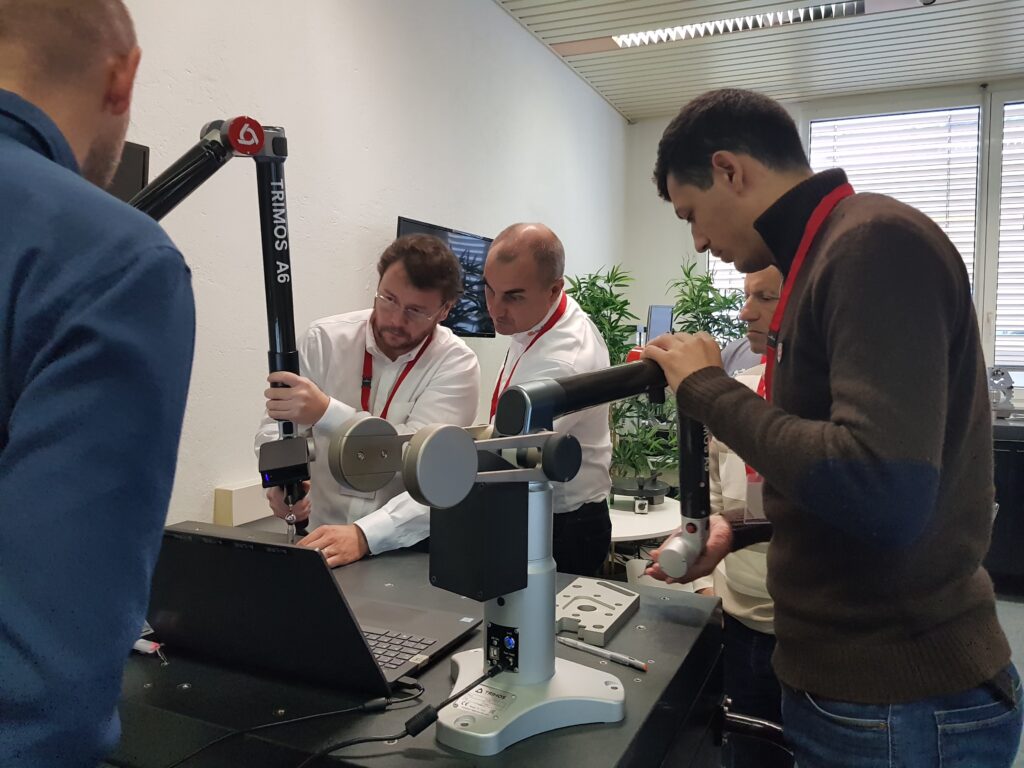
Training Agents nov 2023
12.11.23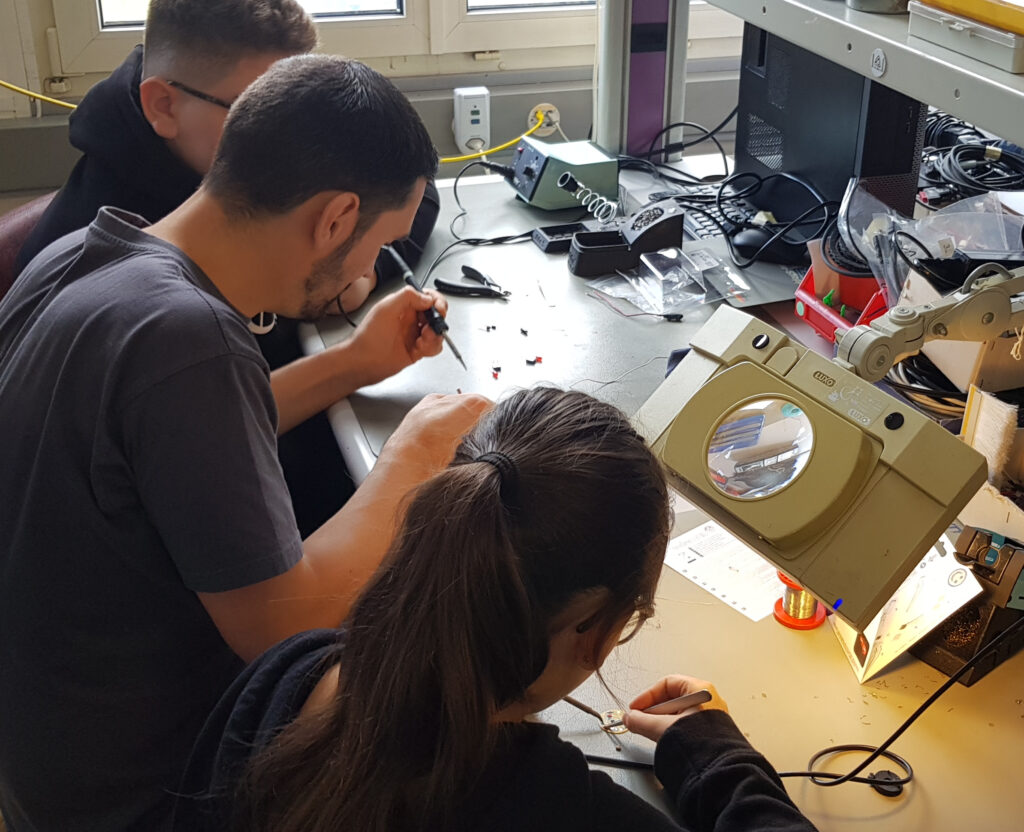
Trades day 2023
9.11.23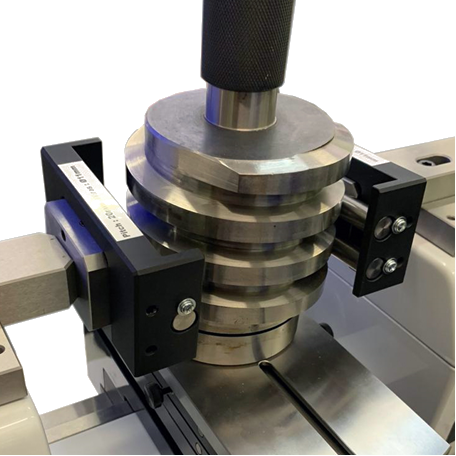
Large Trapezoidal Threads Measurements
10.09.23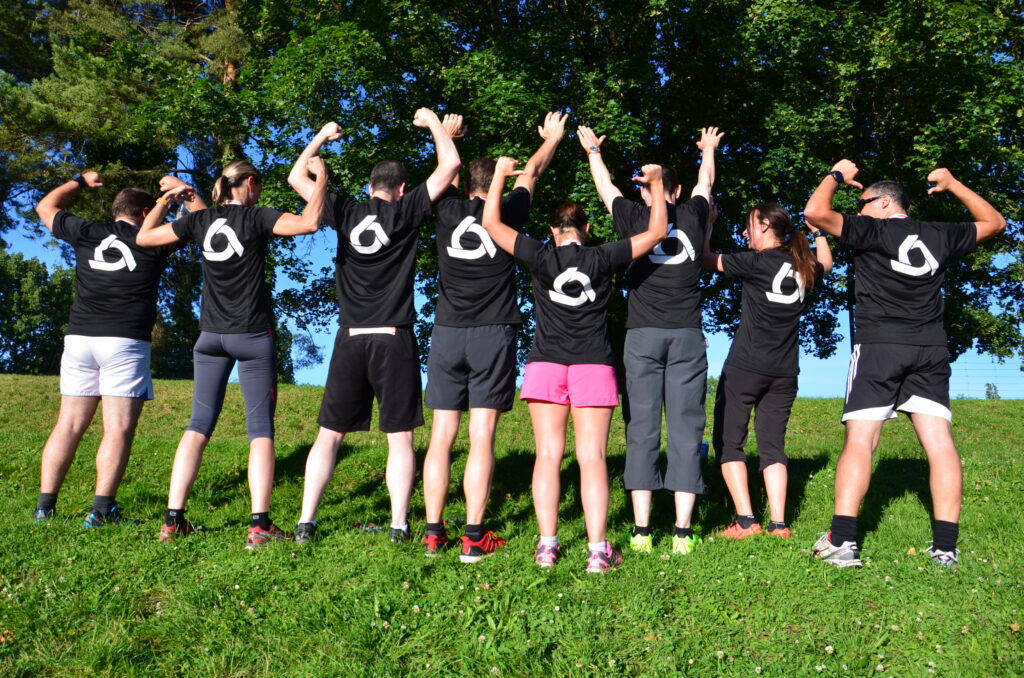
Trimos Shines at B2Run Race in Lausanne
18.06.23
Show more